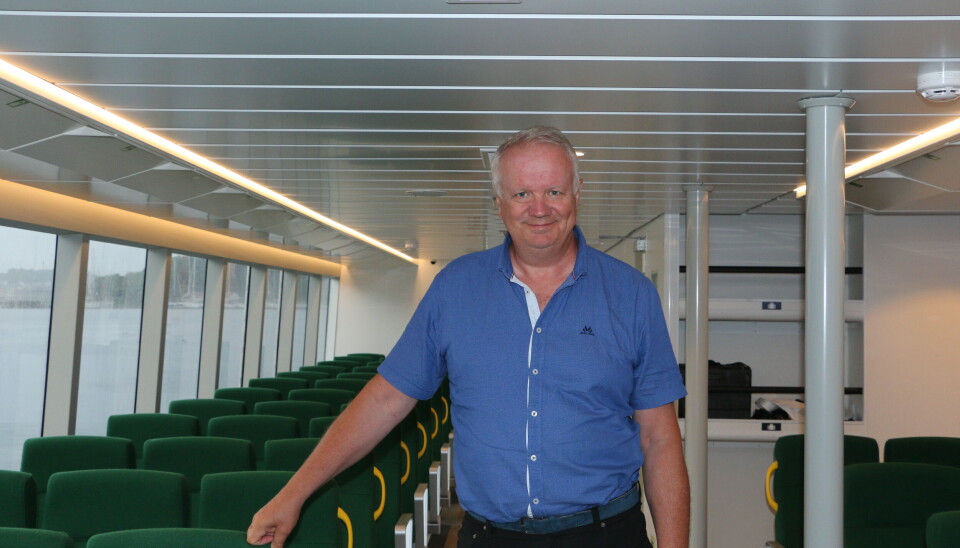
It's all about weight, weight and more weight
Edmund Tolo has extensive experience from building fast ferries, and building Ship of The Year winners. In 2014, Fjellstrand built the world's first electric ferry "Ampere", and this year they have delivered the world's first electric fast ferry.
But if one is to manage to solve the challenge of getting an electric passenger vessel to break the magical 23-knot limit, the weight must be reduced, above all else. The project has succeeded in this, and "Medstraum" has reached a speed of over 27 knots during testing.
Much of the experience Fjellstrand had from building "Ampere" could also be used in the development of this year's winning vessel, explains R&D Manager, Edmund Tolo.
“Fjellstrand has moved into the market with battery operation, not just with "Ampere". We have hybridised a number of offshore vessels that are now in use within the offshore wind industry. But it was "Ampere" that formed the basis for the regulations that came into DNV and that were developed in parallel with us building it.”
Another element Tolo highlights is the long fast ferry experience Fjellstrand has.
“There wasn't much of that experience among those who dealt with systems and integration of battery systems. Charging plugs and charging systems are large units that are based on land plants with the operation of cranes etc. which we used on "Ampere". They require a lot of volume and have a high weight. We knew that it wasn't just us who had to develop, but we had to bring in suppliers who also wanted to develop. They also have to see a market that is coming, and then they have to look at it a little bigger so that they are willing to put in the work needed to develop their product further.”
"Medstraum" is packed with new technology and new solutions. The hull itself is of a completely new design and has been developed especially together with HSVA in Hamburg, in addition to universities in Scotland and Athens, and together numerical calculations have been made where small changes in the hull have been looked at. As many as 2,000 different hull shapes have been tested through CFD analysis. Thus, it is extremely optimised for this particular vessel.
“It was necessary to do, because on board a diesel vessel you have a different weight ratio, and a different cost aspect. There is more to be gained from optimising this vessel because the battery pack is such a large part of the cost and weight,” says Tolo.
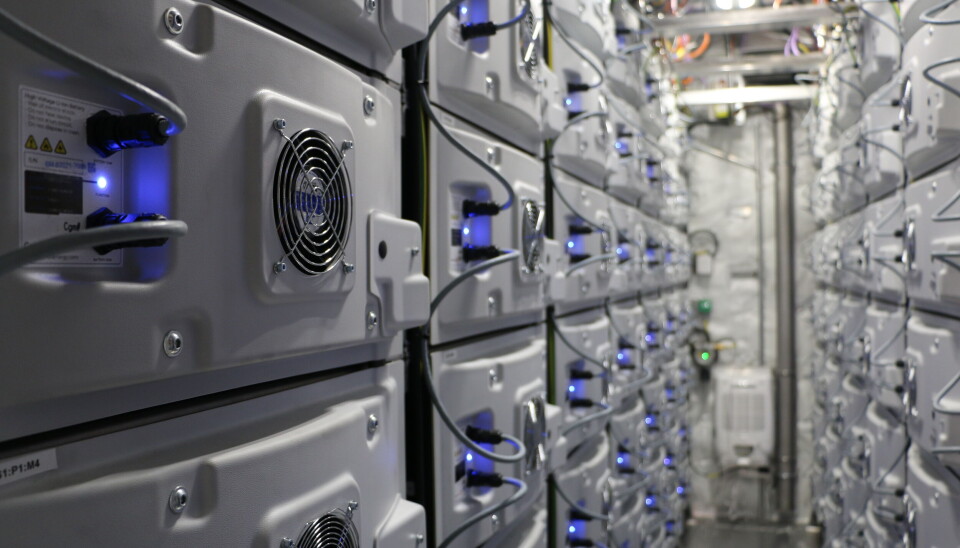
Another innovation is the propeller installation from Servogear, which has been given the opportunity in this development project to optimise the plant and bring out a solution that they otherwise would not have had the time or opportunity to do.
“This means that we have got a propeller system with an efficiency that Servogear says they have never seen before, and is significantly improved compared to before.”
A boat is more than individual components
As everyone knows, a boat is not just individual components. It's about how you put them together to create the best result. During development, several studies have been carried out to optimise the weight of charging systems, cabinets and components on board and what can be left on land. Overall, a light vessel has been created.
A third element is modularisation, where it has been looked at how to make the vessel in such a way that parts of the production can be reused in larger or smaller vessels.
“Only when building a new vessel will we see if we have succeeded in creating a system where both engineering and construction will benefit from what we have been through,” says Tolo.
He says that right from the start the vessel should both look like, and be experienced as, a fast ferry with recognisable factors. The only difference is that it is silent.
“Ease of use must be the same. We must not optimise ourselves out of it,” emphasises Tolo.
Had to be long
But if you see "Medstraum" next to the vessel that operates the route today, there is a fairly obvious difference. Namely the length. Studies showed what the optimal length of the vessel was.
“When the boat became longer, it again led to us being able to have space for the batteries above deck. We believe that is a very good solution. Since this must meet the fast ferry code, there is little space down in the hull for the battery, and so it was natural to look above the deck. You can say that it is a shame to use an area where there could be room for passengers, but this one has room for the number it should have. If you want to have an extra 100 passengers, you have to build a bigger boat,” says Edmund Tolo.
He is unsure whether the solution of placing the battery rooms above deck, far from the ship's side, will become the future industry standard. But what they have seen in the project is that it reduces the risk in connection with a collision where water can get into the hull.

“Today, only leak stability is considered when it comes to collisions. But when we look at it, there is a risk of fire if seawater gets into the battery compartment. It is the same thing we do here as when you place the petrol tank in the back of a car. It's about having it in a place where there is the least chance of damage. Everything becomes easier when you get it over the top,” says Tolo.
Got design help from Hareide
The design of a vessel is also about appearance, and how we as travellers experience it both from the outside and from the inside. How can that be solved in a project where weight is such a decisive part of the result? The answer was to look back to "Ampere", explains Tolo.
“When we built "Ampere", we envisioned a ferry of that size, and stripped away everything we didn't need. We have done the same here as well. We took away everything except the passenger lounge, and then we added everything that was necessary for it to be approved for use; as a universal design, the practicality of running from port to port, and then it looked the way it does.
But from the side there was also help from a highly recognised and experienced designer, Einar Hareide, who is perhaps best known for his car designs from his time at Swedish SAAB. Among other things, he was behind the design of the SAAB 900 and SAAB 9-5. But he also has experience from ship design.
“He came in at the end to make it look right,” says Tolo and laughs. “We think he has done a very good job and we have come away well from it in terms of appearance.”
Because the key words here have been weight, weight and, again, weight?
“Yes, that's a keyword. You could have a kiosk on board, but it costs money to transport back and forth on the route and this type of route does not have such a need for one.”.
Covid put the brakes on
It's a theme that's hard to escape when you're sitting on board an award-winning vessel, built during a worldwide pandemic. Not only have they kept the budget, they also delivered the vessel fairly on time.
“The Covid-19 pandemic meant that we took some more time before we dared to enter into the contract. We had a delay in the project by ensuring that we were actually able to build the vessel, but we have come out of it with not too many delays after all.”
Tolo says that they are very satisfied with the collaboration with Kolumbus, who also dared to start the project in the middle of the pandemic, and participated and shared the risk.
“With new development, there is a higher risk of something going wrong. A shipping company does not have the opportunity to adjust requirements along the way and must take a greater risk. For Kolumbus and similar mobility companies, this risk is reduced and the possibility of being able to reduce the financial risk if, for example, the speed or other requirements are not achieved.”
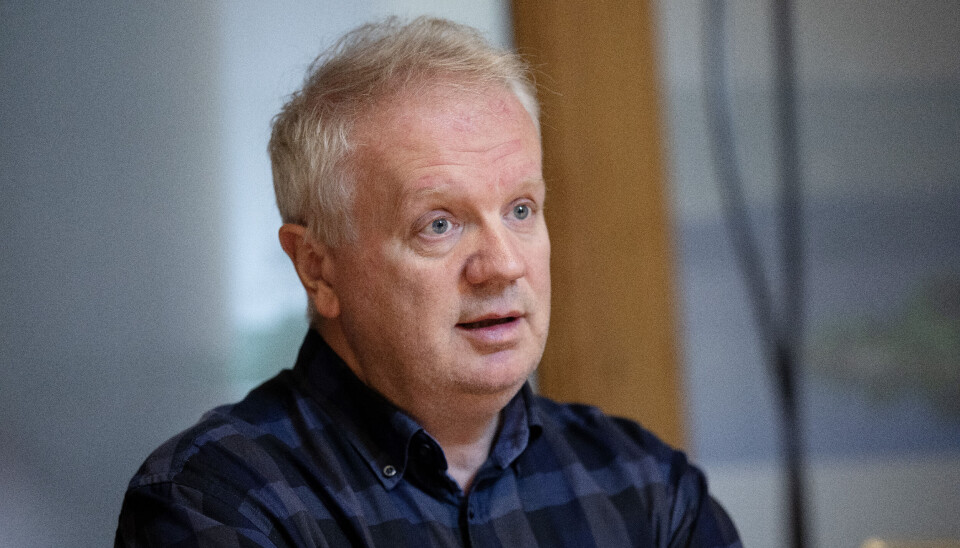
Kolumbus entered into a contract with Norled for follow-up of the construction work. According to Tolo, this gave them the user expertise to get the vessel the way they want it.
He also highlights the work Maritime Cleantech has done in bringing together those who will work together.
“They managed to get hold of the right partners, which we might not naturally have chosen if we had followed the familiar country road. So even though we feel a greater risk by working with foreign universities, we have received many new impulses. I assume that the others have also received it.”
And one must conclude that they have succeeded, as the revolutionary vessel has been created within a year. A year that also includes a worldwide pandemic.
What does it mean to you to win again?
“One thing is that it means something for self-esteem, but that it will also mean something in terms of the market is quite clear. If we look back at "Ampere", it took too long between the time it was delivered and the arrival of new contracts. Everyone chose to wait and see how it went, and in the meantime our foreign competitors could copy the technology. That must not happen again. We know this works and it was not developed by chance. All you have to do is start buying from Norwegian shipyards right away. Both the shipyard and supplier industry depend on it,” concludes Tolo.