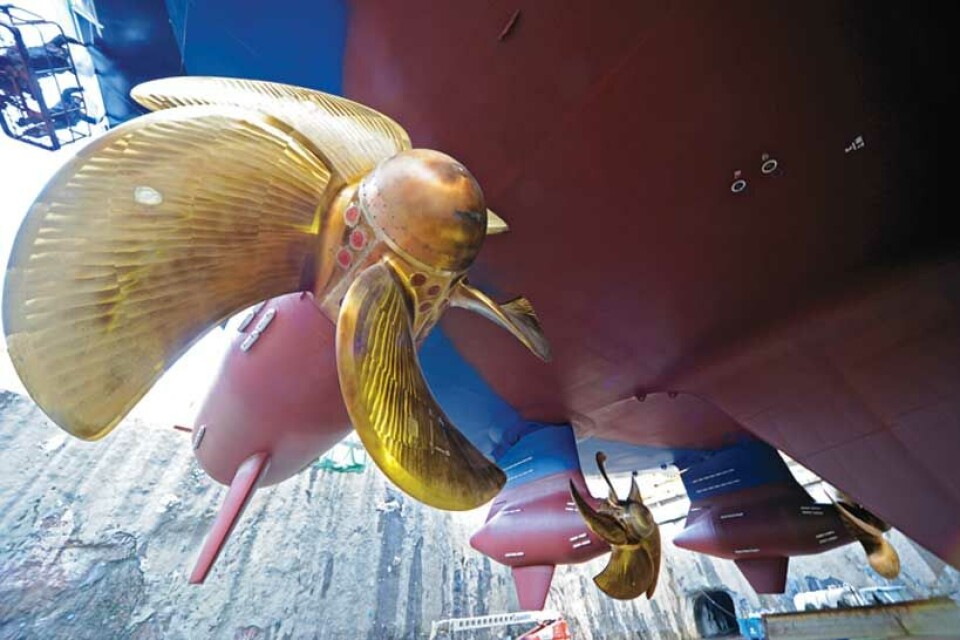
Azipod propulsion drives take the next step
ABB Marine’s Azipod propulsion systems are installed on more than 100 vessels including cruise ships, offshore vessels and icebreaking vessels operating in the harshest Arctic conditions. In April the group launched the Next Generation Azipod XO pod design.
Denne artikkelen er tre år eller eldre.
ABB Marine’s Azipod XO pod, assembled in Helsinki, offers a near-10% improvement in fuel efficiency and new bearing and seal arrangements allow servicing and replacement to be made from inside the pod. They have produced improved operational performance, enhanced reliability, better maintainability and higher environmental protection and the combined results of the improvements can provide up to a 50% reduction in maintenance costs.
Celebrity Cruises’ fifth generation vessel «Celebrity Reflection», which is under construction at Meyer Werft in Germany and due for delivery in 2012, will be the first of the operator’s five sisterships to be fitted with the new XO pods. In addition, Norwegian Cruise Line has agreed a US$50m deal for Azipod XO drives for its two newbuildings ordered from Meyer Werft. The vessels, each comprising 143,500 tons gross and capable of carrying 4,000 passengers, will be the largest cruise ships to be built in Germany.
A key element in Celebrity’s decision was the requirement to reduce fuel consumption and equipment costs. The propulsion power was reduced to 2x17.5 MW from approximately 2x20 MW and the maximum speed of the vessel is some two knots less than the speed of the earlier vessels. The speed was also affected by the vessel’s larger main dimensions. However, the smaller Azipod units performed as well as the previous larger pods and the difference in power input was gained through the higher efficiency of the new XO pod in spite of the smaller torque of the motor and the smaller propeller diameter.
– ABB’s comprehensive solutions for our shipbuilding customers ensure reliable power supplies onboard, as well as technologically advanced propulsion systems that help big ships navigate quickly and safely, using less fuel, said Veli-Matti Reinikkala, head of ABB’s Process Automation division. – Our equipment helps cruise operators cut down on fuel consumption and reduce their carbon footprint. The technology ensures the comfort and safety of passengers.
The propulsion efficiency of Azipod propulsion, installed originally on Carnival Cruise Lines Fantasy class cruise ships «Elation» and «Paradise» in the mid-1990s, improved by around 9% when compared through full scale measurements with earlier identical sister ships with traditional shaftlines. Since then ABB Marine has improved the system by another 9%.
With changes to the shape of the Azipod and through hydrodynamic optimisation of the positioning and angular placement of the pods when integrated with the hull. When designing the new XO pod, ABB Marine achieved another 1.5-2% improvement compared to the best available designs, representing an improvement of 9% of the Azipod during its existence and a total improvement of some 18% in propulsion efficiency compared with that of shaftlines in the mid 1990s. ABB compared shaftlines with Azipod propulsion through model tests last year at Marin in The Netherlands which found that Azipod propulsion compared to latest fixed shaftline propulsion designs still had a 6% - 8% percent lead in propulsion efficiency.
Jukka Varis, Vice President, Product Management Propulsion Products, in charge of research and development work of the Azipod, ABB Marine said that despite some
20 years’ experience the group knew it would have to start from the beginning in order to achieve real development when designing the second generation Azipod though it was able to utilise proven technology from first generation pods or from other applications.
Factory workshop tests at the VTT Technical Research Centre of Finland last year focused on different types of thrust bearings, the sliding bearing primarily intended for the new XO pod and a roller bearing version of current type for comparison and for retrofit purposes. The two bearings were rigged against each other with a rotating shaftline in between, and tested for full load, 1.6 times full load and almost 2.5 times the loads expected from real operation. Rapid load changes were also applied to simulate changing operating conditions. Using hydraulics, both axial and radial forces were induced.
– The roller bearing has typically a minimum oil film between the surfaces of some 2 µ to 4µ, or 0.002mm to 0.004mm, said Mr. Varis. – With the sliding bearings tested the minimum thickness was some 40µ even with higher loads. We did continuous measurements of this film thickness, which proved sufficient even during our toughest impact tests, which simulated extremely heavy ice loads. The tests convinced us that the sliding bearing design has a very good safety margin for normal static and dynamic loads foreseen, against the unacceptable situation where metal would begin to slide against metal.
The new seal design developed for the new Azipod drive can be changed from inside the pod by using a temporary inflatable seal placed around the pod but this method is for an emergency situation as the seal would normally be changed during a dry docking, said Mr. Varis said.
The concept for azimuthing propulsion using a variable speed electric motor placed inside the propeller pod, which is controlled by frequency converters onboard the diesel-electric vessel was developed for an ice-going vessel in Finland. The turning pods make the vessels particularly manoeuvrable and by going astern, with the Azipod propulsion units “ahead”, less energy is needed for the vessel to proceed through ice thanks to the pods that suck and blow the ice away from the vessel hull.
Azipod propulsion has recently been fitted on five Arctic 70,000 dwt shuttle tankers, built in South Korea and in Russia, and is used on a series of Arctic container ships built in Finland and Germany, all operating in Arctic Russia. In all, some 30 dedicated icebreaking vessels use Azipod propulsion today. – If we can dimension the Azipod to reliably operate in conditions where its pod and propeller hits several metre thick ice blocks, it makes the task of dimensioning pods for open water operation much easier.
Last year ABB Marine introduced the concept of long term service agreements. – It should be possible to serve, and even replace, the most critical components without dry docking the vessel, said Antti Ruohonen, Director, Propulsion Products Services. – We developed a new type of shaft sealing which can be replaced from inside the pod, without the need for dry docking. We developed the sliding thrust bearing in a way that allows the wearing parts, the thrust pads, to be replaced from inside the pod. It takes one day to replace the seal and the thrust bearing components can be replaced in about eight hours meaning critical parts can be replaced during a normal port call. Also the turning shaft seal, placed between the ships hull and the vertical pod structure, can now be changed from below and even without dry docking, provided the vessel can be trimmed in such a way that the upper part of the pod can be raised sufficiently above the water surface.
– We tell the client that we believe service will cost a certain amount during the first five years, and this much during the following five, including dry docking service, work and spare parts. If it costs more than expected, the customer will not see this. All maintenance tasks, spare parts and service are agreed on beforehand, in one package, and Azipod service and maintenance procedures are scheduled beforehand. Agreed checks prior to the planned maintenance activities ensure smooth maintenance aiming at eliminating any unscheduled downtime with unnecessary costs.
ABB recently established a dedicated US-based Azipod Service organization and a range of Azipod service products. Service operations are overseen from ABB Marine’s service centre in Miami. ABB also has a network of dedicated centres in Houston, Murmansk and Shanghai where operations started in February and the group now employs 15,000 people.
Joi
nt project
Last autumn ABB and Eniram Oy announced a research and development study to optimise the energy efficiency of Azipod installations onboard vessels. The joint project is based on the finding that further fuel consumption savings can be reached by optimising the toe (steering) angle of the installed Azipod units, in addition to the angle optimization done already at the design stage of the vessels. It is estimated that the fuel consumption of the vessel can be reduced by up to 2% by optimising Azipod toe angles. The savings reached have been evaluated and verified by the partners which are to develop and manufacture intelligent systems providing Azipod toe angle optimisation in real-time operation based on the Eniram’s VMS Vessel Management System) currently developed for optimisation of the vessel’s trim. The system is to be applied on both newbuildings fitted with Azipod propulsion as well as on existing vessels.
– When looking at the pod drive only, the initial investment cost for an Azipod is higher than for a shaftline, a propulsion drive and a propeller, said Mr. Varis. – But, in all, when looking at the installation costs, with installation work included, lining long shaftlines and shaftline bearings, the investment in and installation of eventual stern tunnel thrusters, and of continuously more sophisticated rudders and steering gear, with all cables needed, I do not believe that the Azipod is more expensive than traditional diesel-electric propulsion.